CTSD Manned Vacuum Chamber Laboratory
Vacuum Chambers in the Building 7 Highbay
The Branch arranges for visitor badges for retirees who haven't joined the retiree organization. It isn't difficult to pick up the special badge before
entering the site though. The security folks have the badges ready. Imagine how many times I entered this door to the Building 7 High Bay lab during my
35 year career. This door is on the site north end. There are doors on each side with double doors opening into the Building 7A lobby.
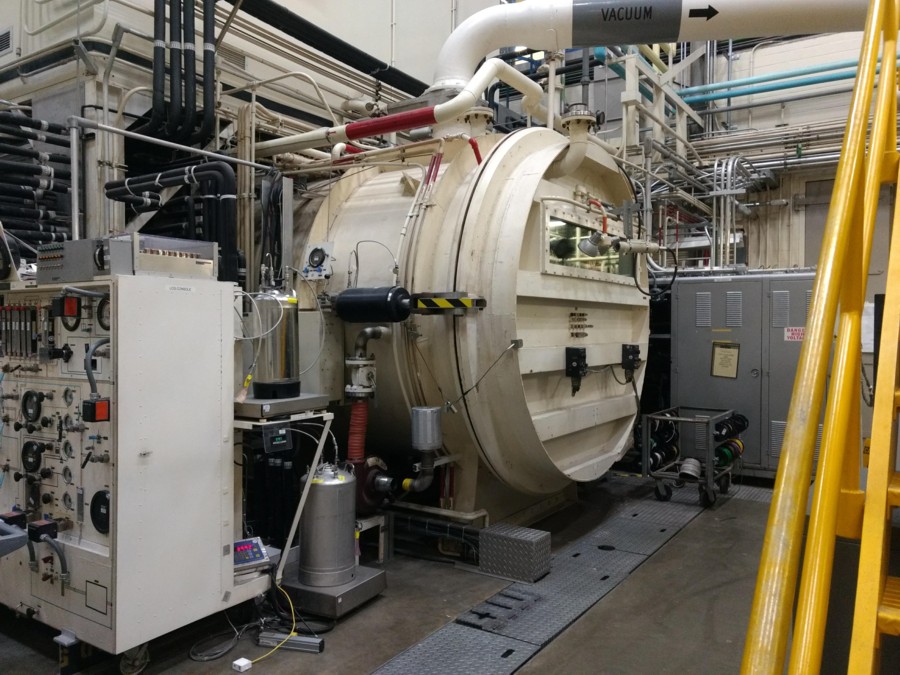
The 8-ft chamber was the first operational chamber in Building 7 of the L B Johnson Space Center (formerly the Manned
Spacecraft Center). The chamber was a surplus Air Force pilot training chamber. It had been modified by cutting off this end of the chamber and
installing the door to allow large test articles to be installed. This was the chamber where Jim Leblanc lost suit pressure while at vacuum and was
exposed to a pressure at least as low as 0.25 psia and probably lower. Since he felt saliva boiling off his tongue just before losing consciousness, he
must have been below the triple point of water somewhere in the 5 - 10 Torr range. Loss of consciousness occurs about 14 seconds after the pressure
in the lungs falls below about 1.75 psia (as I recall). The oxygen partial pressure in the lungs will be less than that because the lungs are at saturation
pressure with water vapor and carbon dioxide. The partial pressures of those three gases add up to the total pressure.
Video demonstrating the "triple point" of water.
Suit Pressure Loss Video. NOTE: There are only FOUR
segments of this video that actually relate to the suit pressure loss accident: The two color videos where Cliff and Jim speak to an interviewer, the actual
video recorded from the 8-ft Chamber CCTV, and the B&W photo of the guys receiving a commendation certificate for the rescue. Everything else is
video of other chamber facilities and personnel who had nothing to do with the incident. BUT NOTE THIS: At the beginning of this video two guys in
white lab coats are entering a vacuum chamber that may be the 11-ft Chamber just after its delivery to our building or perhaps before it was shipped or
it might just be an identical chamber. But in any case, the 11-ft Chamber wasn't installed in our building until after the suit pressure loss
incident.
Here is a well written article in the University of Houston's radio and web series "Engines of Our Ingenuity." I listened to episodes nearly every day as I drove to work. The only error I see in this one is that Jim Leblanc is referred to as a "technician" when he actually has a degree in mechanical engineering. An early report made this mistake, and it has been copied by most later writers. The Body at Vacuum
Playtex and International Latex and NASA spacesuits: The Girdle-Inspired History of the Very First Spacesuits
Many developmental and manned certification tests of the Apollo portable life support system (PLSS) were performed in the 8-foot chamber. There are some good photos of astronauts during dry runs in the chamber in the 50-years-ago page linked here. The counter-weighted weight relief system was something I had forgotten about! NASA features Ken Mattingly in the 8-foot chamber in this history from 50 years ago.
Ken Mattingly served as a test subject
for several of those tests. In this excerpt from T. K. Mattingly's interview for JSC's oral history project he describes his space suit vacuum testing experience with us in CSD:
NASA Oral History
"I remember that since no one else wanted to do these things, that I got to be a test subject.
They had a professional test subject, Jackie [Mays]. I can’t think of his name now. Jackie—big,
strapping, tough guy. I was a scrawny little runt. One of the deals was, space suits were rare and
expensive, and so, you know, you didn’t make space suits for the test subjects. You made space
suits for flight crews, and then the test subjects would try to find the one that was closest to the right
size.
"Nothing fit me, and so I had Frank Borman’s suit. Frank Borman and I are not the same size
in any dimension, and it was really miserable in there. Old Jackie would help me. He was teaching
me the ropes, being a test subject. So we got to be pretty good friends. As I learned more about it, I
started getting involved in writing some of the test programs, since we built this. We sort of
designed the requirements and the system together, then we kind of wrote the test program. It was
just, just really fascinating. That bunch of people at Crew Systems was really, really a lot of fun."
NOTE: Jack Mays was the lock observor (rescue tech) during my suit run. The lead photo shows him standing beside me as I sat during the prebreathe. He was a good friend of Jim Leblanc. Jack died a few years ago. - JMS 12/29/19
Later, the Apollo-Soyuz Docking Module test article was tested in this chamber culminating with a joint manned test with American
astronauts and Russian cosmonauts. Look at the mission patch at upper left (assuming my HTML code works) and see that the Russians put Soyuz
first in their name for the mission while we put Apollo first.
As the Shuttle program got under way, the Shuttle urine dump nozzle was tested in the 8-ft chamber. That required the installation of a shroud cooled
with liquid nitrogen. Cleaning the frozen urine off the shroud was a smelly job. Having volunteers contribute to the test while in the chamber airlock
didn't work well, so big plastic jugs were placed in the Men's Rooms for urine donations. The urine was then transferred to transfer tanks for dumping through the dump nozzle.
The work then shifted to unmanned development and certification test of the new Shuttle PLSS. Any new or refurbished PLSSs are now certified at the
Hamilton Standard manufacturing facilities and this chamber is no longer in use.
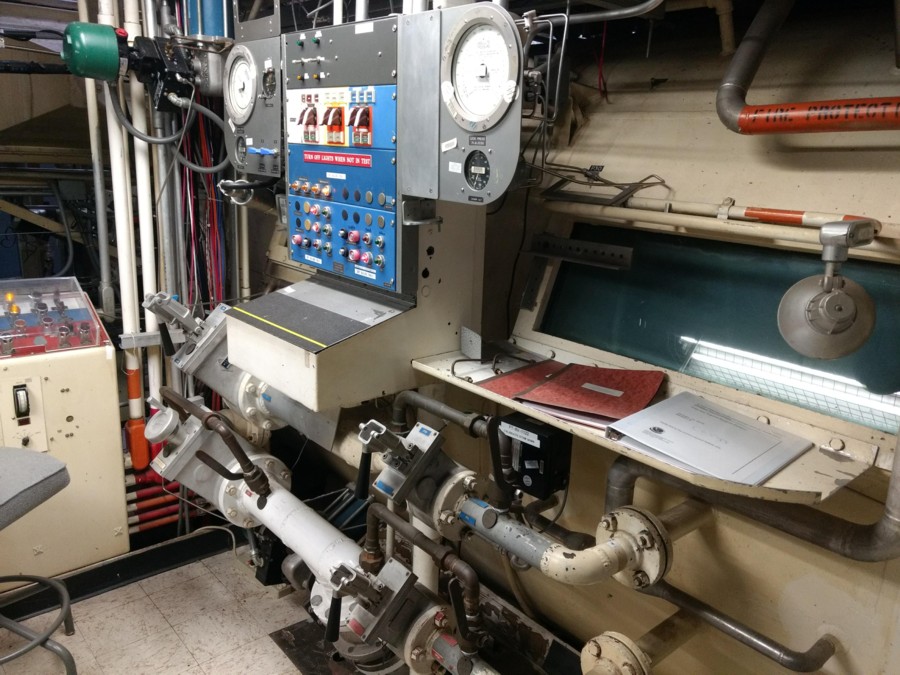
This is the chamber control console with manual valves for depress and repress of the chamber. It had aircraft rate-of-climb and altitude gauges in the
old days. The panel had to have a vibrator to make the gauges work. The vibration was required to overcome the drag/friction in the gauge mechanism.
There was enough vibration in the aircraft to take care of that.
The only instrument we had for measuring very low gas pressures with any precision was a McLeod pressure gauge. The gauge used mercury and required a trained operator to get an accurate reading while preventing mercury blow-back into the chamber. "The McLeod Gauge measures the vacuum pressure in the range between 10-1 and 10-5 torr. This can be used as a primary standard device for calibrating other low-pressure gauges." The McLeod gauge that we had was simpler to use than the one in the linked article.
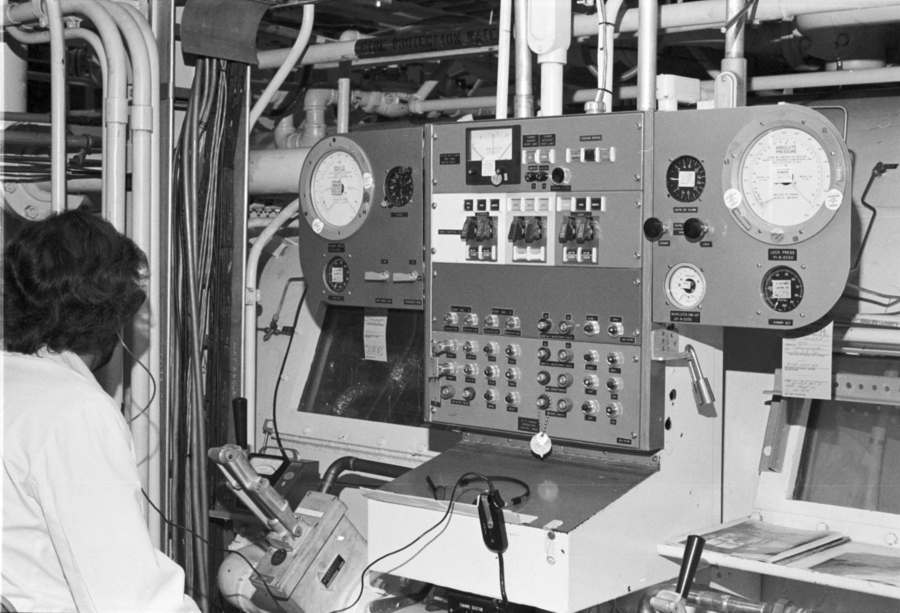
This is a view of the 8-ft Chamber Operator's Console back in 1976.
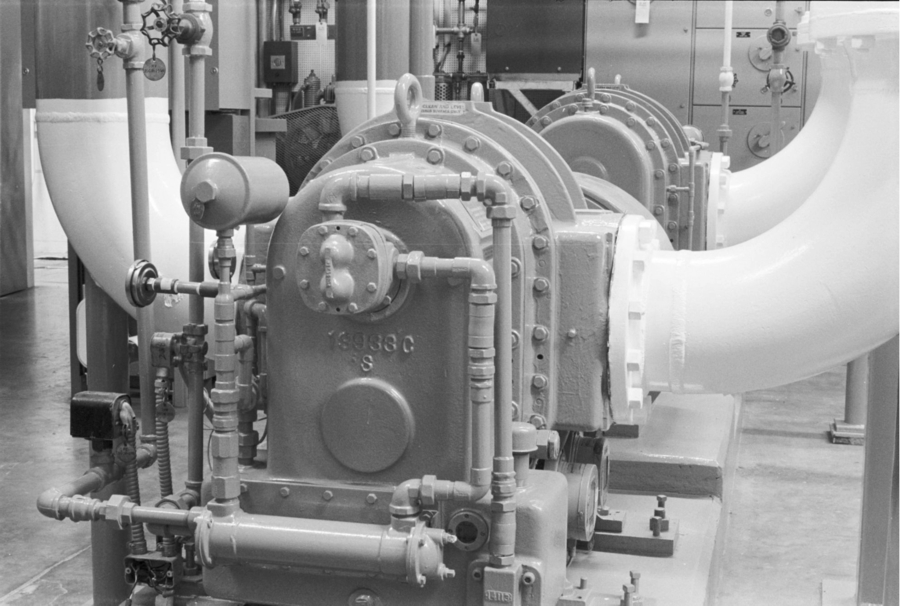
These vaccum pumps could be used for either the 20-ft Chamber or the 8-ft Chamber. They were called "blowers" and, as I recall, they were manufactured by the Roots company, the same company that made the mechanical superchargers for race car engine air intakes.
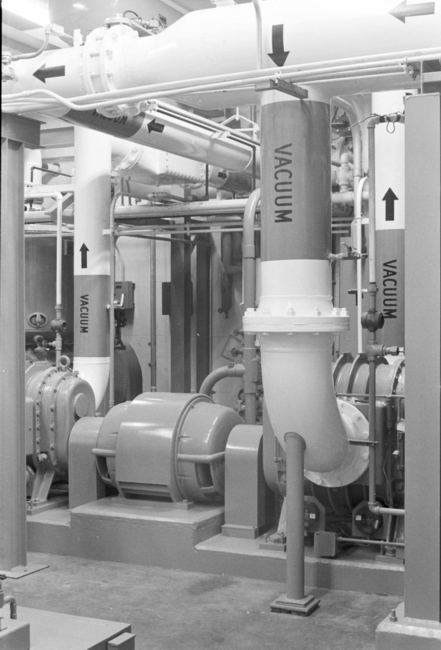
Here is a side view of the blowers. I don't have photos of the "roughing pumps" at hand, but the roughing pumps reduced the chamber pressure to something like the pressure equivalent to about 50,000 feet before the blowers could be started. Chamber depressurization was usually pretty slow by the time the blowers could be brought on, but then depress to vacuum was fast. (In the upper left near the top of the photo is a grey, vertical cylinder which was the oil reservoir for one of the roughing pumps if I remember correctly.)
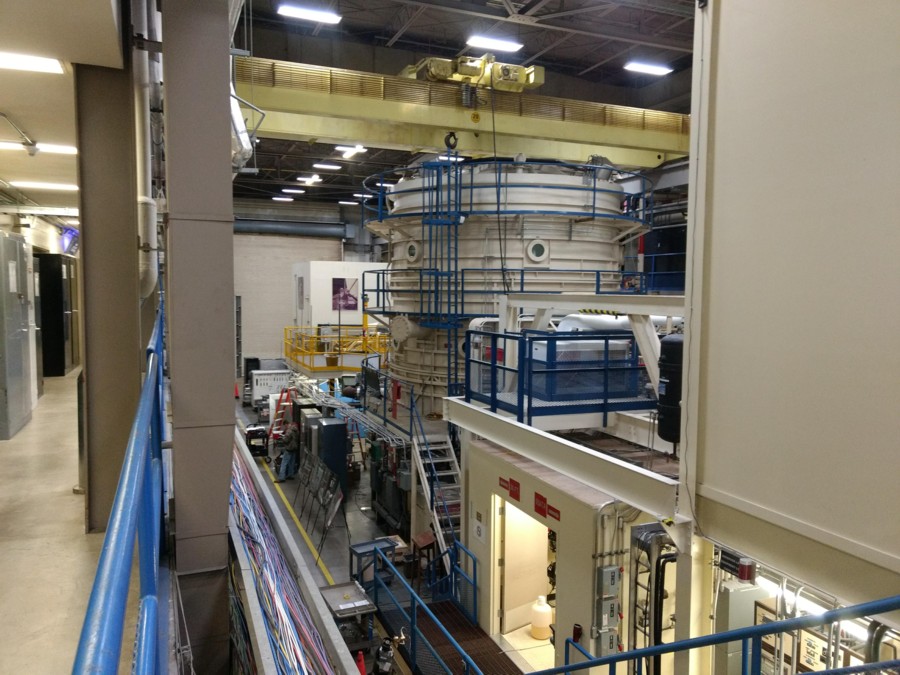
At one time long ago I was able to get a photo of the full length of the highbay, but too much has been added for that to be possible now. In the
distance is the 8-ft Chamber with the control room above it. The 20-ft Chamber occupies the remainder of the view. A section has been added to the
20-ft chamber to make it taller; but there is still room for the crane to lift the top lid of the chamber. The SSATA (Space Station Airlock Test Article)
was added to the 20-ft Chamber outer lock on this end and there is a big room over it with a lifting device to allow the SSATA lid with crewmembers
suspended from it to be pulled up to safety in case of emergencies.
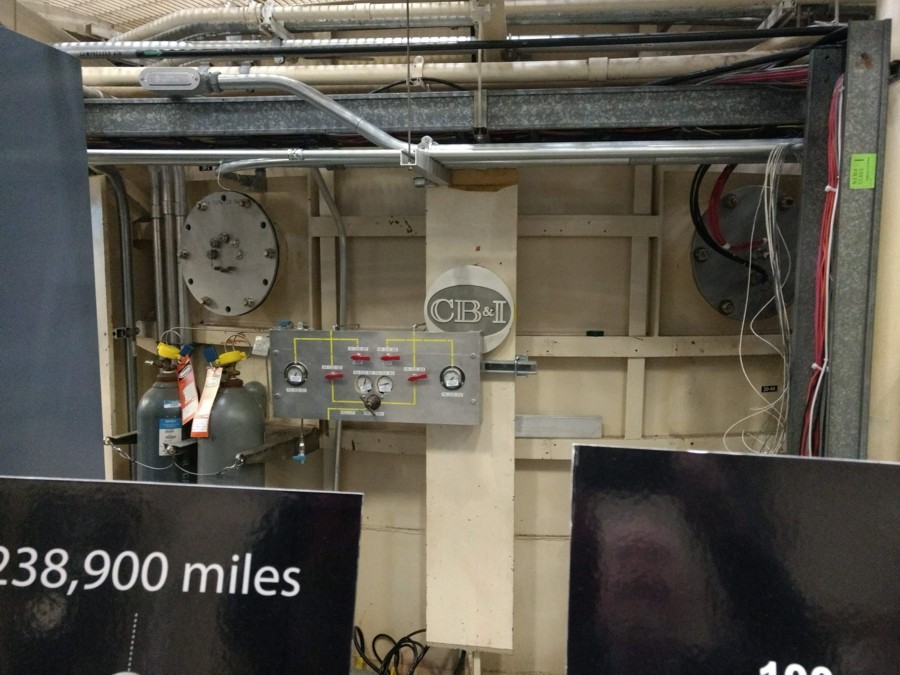
The 20-ft Chamber was under construction when we moved onsite in 1964. Chicago Bridge and Iron was the contractor and
their original plaque is still there. This photo shows the iron bands that girdle the iron cylinder of the chamber to strengthen it for a 14.7 psi differential
pressure from outside to inside. That is 14.7 psia normal atmospheric pressure outside and 0 psia inside. Zero psia in this case would be about
0.001 Torr.
This was the chamber in which I was a test subject for a test of the Gemini spacesuit visor in 1965 prior to the first U.S. EVA on Gemini IV with Gus
Grissom and Ed White. Gemini Spacesuit Vacuum Test for GT4
The Skylab Medical Equipment Altitude Test (SMEAT) 56-day test with Bob Crippen, Bo Bobko, and Dr. Thornton was conducted in the 20-ft
Chamber. SMEAT Test
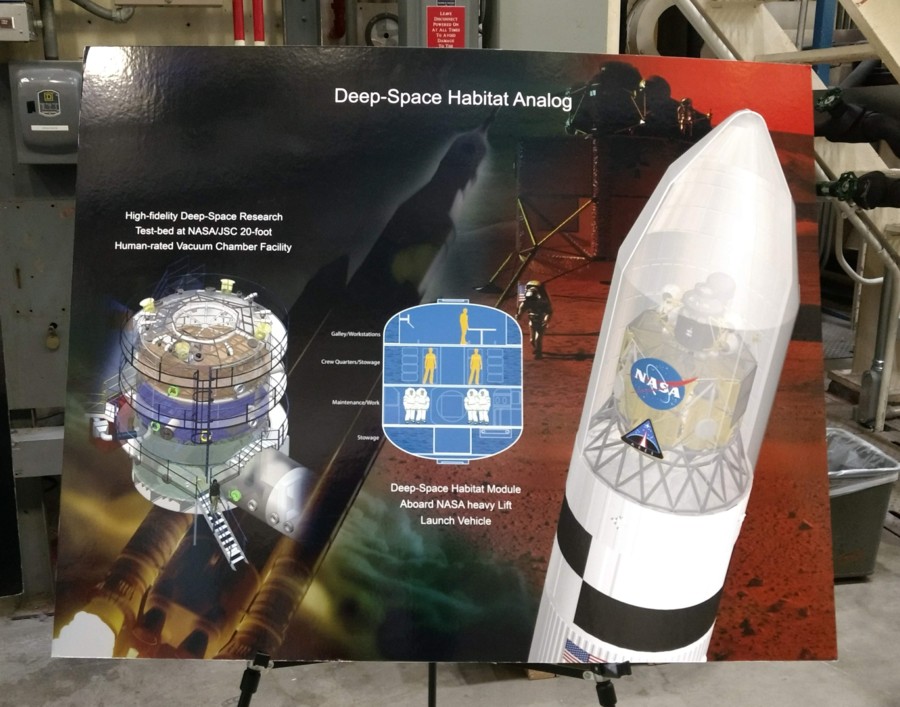
A new prebreathe protocol test is planned for the 20-ft Chamber. The vertical cylinder will have three levels as was used in a 90-day manned test to evaluate long-term ECS and living quarters requirements for a group of crewmembers. This test would evaluate a new pressure and prebreathe protocol for a future habitat that would be occupied by a group of astronauts on the moon, in lunar orbit, one of the LaGrange points, or wherever. The proposed operating pressure would be 8.3 psia with about 30% xygen. The hypothesis is that a crewmember living in that gas pressure condition could don a suit, do a quick purge to get the suit air mixture to at least 85% O2, and then immediately do an EVA with a
suit pressure of about 4.7 psia without having to do a lengthy prebreathe. There will be no suits in this test though. The crewmembers would don oxygen masks supplied by 85% oxygen mixture and the entire chamber would be reduced to 4.7 psia (suit pressure) for the duration of an EVA. The chamber pressure would then be increased again to 8.3 psia and this would go on for 11 days. In addition to the crewmembers, there would be two medical techs along to do doppler
checks to see whether the crewmembers were getting gas bubbles in their blood which, of course, would be a sign of inadequate prebreathe and the
possibility of getting the "bends."
Good article on suit pressure and prebreathe.
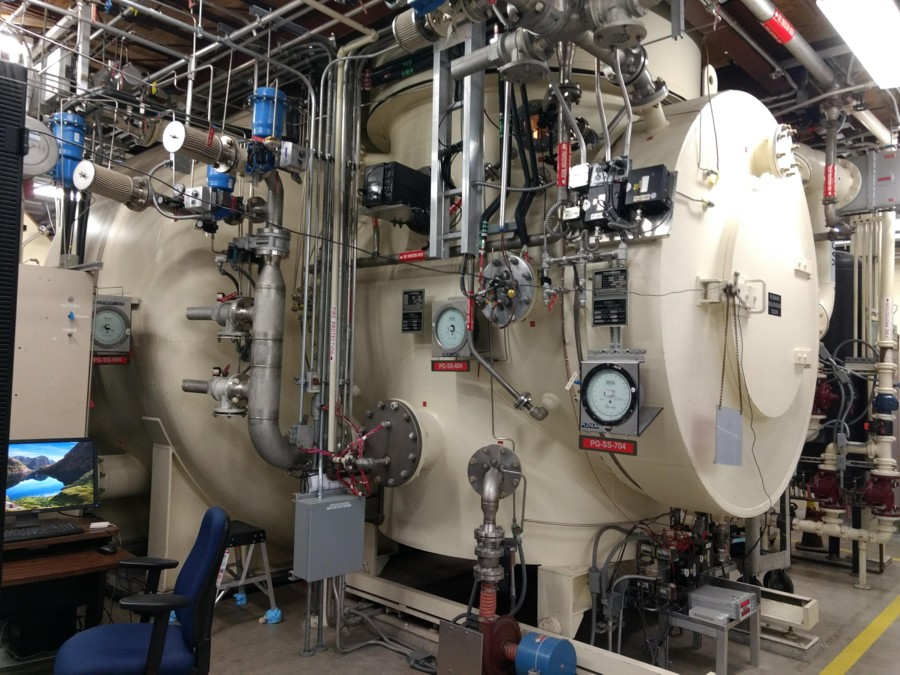
This is the outside view of the SSATA (Space Station Airlock Test Article) that was built onto the end of the original airlock for the 20-ft chamber. It
was under construction in 1997-1998 when I retired. I was in Moscow in January 1998 observing a test of the Orlon Spacesuit at Zvezda Orlon Spacesuit Test at Zvezda when I got news that I had
the option to receive a bonus for retiring. Things were worked out so that I could retire and then be hired back as a contractor for the first SSATA test
that would include both the U.S. EMU and the Russian Orlon in a joint SSATA verification test. They are still doing astronaut vacuum training in the SSATA.
Video of Astronaut dry run in the SSATA
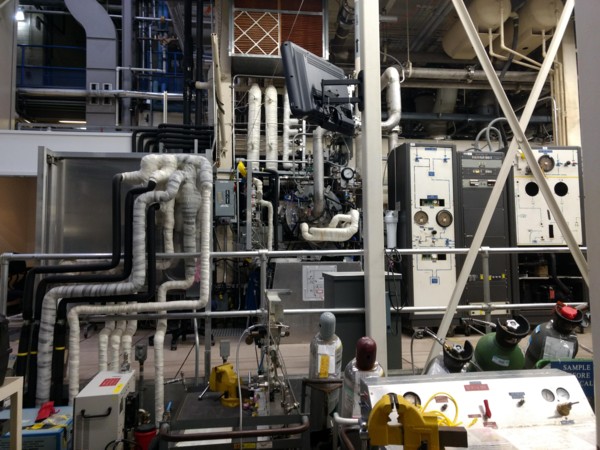
The photo on the left shows the view through the entry hatch of the
11-ft Chamber through the outer lock and inner lock to the "cabin." The cabin had a
flight LM ECS (shown in the photos below) in it when it transported and installed in Bld. 7. Apollo astronaut crew training tests were conducted in the inner lock/cabin from about
1968 through the remainder of the Apollo program. Astronauts could experience walking on a treadmill at various rates to evaluate the cooling capability
of the space suit and its portable life support system (PLSS). There were two treadmills in the inner lock back then, but I don't think we had two
astronauts in the inner lock for one test. We did do LM EVA training in the LM cabin simulator. A pair of astronauts would connect to the LM ECS
(Environmental Control System), then use the LM depress valve to depress to vacuum, and then perform the steps to switch to the PLSS systems to
spend a few minutes at vacuum conditions with life support provided by the PLSS. They then reconnected to the LM ECS and repressed.
A small diameter chamber such as the 11-ft doesn't require extra strengthening outside (or inside) its metal shell. The view on the right shows one side
of the chamber mostly obscured by facility support systems. I forgot to get a photo from the control room side. I do have some in my collection.
Actually, I have too many photos to include in what was just supposed to be a quick look at the current status of Building 7.
When the Shuttle EMU was ready for manned testing in the late '70s, the inner lock of the 11-ft Chamber was modified to support the EMU and the
facility systems needed to provide the support functions for the suit that the Shuttle would have supported. But first, we had to redesign and rebuild the spacesuit system the caused the EMU Fire. This excellent article on the fire was written by Terry Dunn with information provided by Joe Nowetner. Crew spacesuit training runs were
performed in the 11-foot Chamber from 1980 until around 2005 - 2010. The training runs are now done at the 20-ft Chamber SSATA.
After the return of the Shuttle from the first flight, STS-1, our division chief decided to do a demonstration test to show that the Shuttle EVA spacesuit and life support system (EMU) would have worked if it had been needed for an emergency EVA during the flight. This page, Post-STS-1 Manned Vacuum Test of the EMU, describes the unexpected result. The page includes a photo of the 11-ft Chamber Control Room as it looked back then. I am the only person standing in the photo.
When the USA began to recruit female astronauts, we realized that we would eventually need female suit test subjects. This page of Women's Space Firsts includes the puzzling discovery made during those first tests with female subjects. This discovery led to a major redesign of the EMU spacesuit waist bearing. One of those women was Astronaut Kathy Sullivan who was the first woman of the United States to do an EVA. She also trained for an emergency EVA for the Hubble Space Telescope launch. The launch of the Hubble was successful so she (and Bruce McCandliss) didn't have to do the emergency EVA. This is a link to Kathy's recent book about her experience: Handprints on Hubble: An Astronaut's Story of Invention
This article tells about manned vacuum tests of the Orion Launch/Entry Suits in the 11-ft Chamber that were conducted in recent years. Orion Spacesuits Put to a Vacuum Test at NASA (Photos)
Counting Gas Molecules: Glass "tube" resists extreme vacuum pressure.
Radio/TV Vacuum Tubes
From Wikipedia: "A vacuum tube needs an extremely good ("hard") vacuum to avoid the consequences of generating positive ions within the tube. With a small amount of residual gas, some of those atoms may ionize when struck by an electron and create fields that adversely affect the tube characteristics. Larger amounts of residual gas can create a self-sustaining visible glow discharge between the tube elements.[citation needed] To avoid these effects, the residual pressure within the tube must be low enough that the mean free path of an electron is much longer than the size of the tube (so an electron is unlikely to strike a residual atom and very few ionized atoms will be present). Commercial vacuum tubes are evacuated at manufacture to about 0.000001 mmHg (1.0×10-6 Torr; 130 µPa; 1.3×10-6 mbar; 1.3×10-9 atm).[40 C. Robert Meissner (ed.), Vacuum Technology Transactions: Proceedings of the Sixth National Symposium, Elsevier, 2016,ISBN 1483223558 page 96]"
TV/Computer/Oscilliscope CRTs
A CRT is constructed from a glass envelope which is large, deep (i.e., long from front screen face to rear end), fairly heavy, and relatively fragile. The interior of a CRT is evacuated to approximately 0.01 pascals (9.9×10-8 atm)[3] to 133 nanopascals (1.31×10-12 atm),[4] evacuation being necessary to facilitate the free flight of electrons from the gun(s) to the tube's face. The fact that it is evacuated makes handling an intact CRT potentially dangerous due to the risk of breaking the tube and causing a violent implosion that can hurl shards of glass at great velocity. As a matter of safety, the face is typically made of thick lead glass so as to be highly shatter-resistant and to block most X-ray emissions, particularly if the CRT is used in a consumer product.
"The hot-filament ionization gauge, sometimes called a hot-filament gauge or hot-cathode gauge, is the most widely used low-pressure (vacuum) measuring device for the region from 10-3 to 10-10 Torr. It is a triode, with the filament being the cathode."
Ionization Vacuum Gauges for Sale
Video Clips of Astronaut Dry Runs for Shuttle EMU Vacuum Familiarization Tests in the 11-ft Chamber:
Astronaut Dale Gardner with a brief view of me.
Astronaut Robert Springer
Astronaut John Lounge
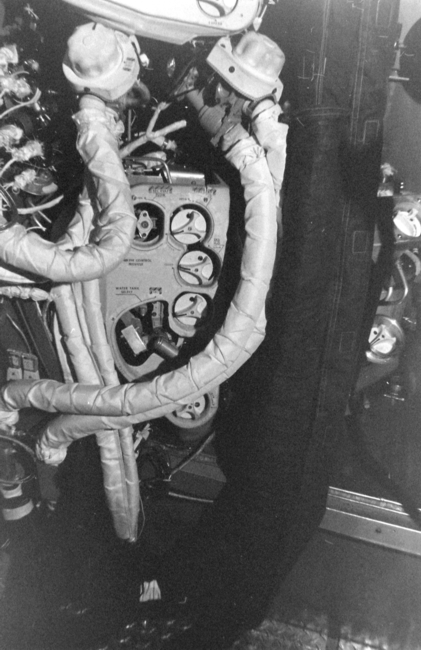
A flight man-rated ECS/Suit Supply unit was installed in the "cabin" of the 11-ft Chamber. These views show most of the Control Panel and then a close-up of the lower part of the panel. Apollo lunar landing astronauts practiced the procedure for transfer from suit operation at cabin pressure in the LM to vacuum at lunar surface pressure. This system was also used to show that the "fix" for Apollo 13 would work. The inner lock of the 11-ft Chamber represented the volume of the Apollo Comand Module cabin in the Apollo 13 test. The LM ECS was removed from the 11-ft cabin when we switced the chamber to Shuttle EMU spacesuit certification and familiarization testing.
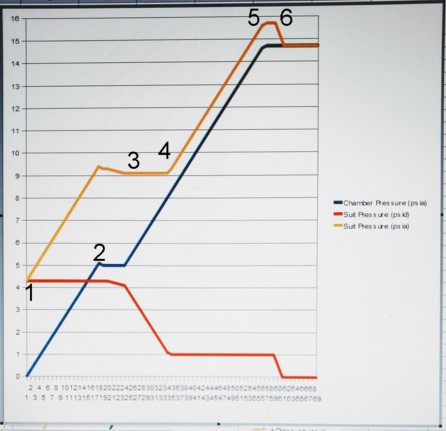
For those who are interested in this sort of detail:
SPACESUIT DEPRESS PROFILE NOTES:
1 Suit O2 Control in "IV" as prebrethe time is up
2 Suit stretches some as differential pressure rises thus reducing absolute pressure in suit
3 When suit delta P reaches relief valve pressure (about 5.1 psid), suit absolute pressure begins to drop with chamber pressure.
4 Depress is stopped at a chamber pressure of 5.0 psia. Suit O2 control is switched to EVA to maintain a suit pressure of no less than 4.3 psid during the depress to and operation at vacuum.
5 Suit delta P goes to relief valve pressure and then absolute pressure drops and tracks chamber pressure
6 Suit pressure slowly drops to the PRESS/EVA pressure control point of 4.3 psid (which is 4.3 psia when the suit is in a vacuum).
SPACESUIT REPRESS PROFILE NOTES:
1 Once safely inside the airlock, the crewmember moves the O2 Actuator from "EVA" to "PRESS." This is to prevent the inadvertent dumping of the pressure from the secondary oxygen supply (SOP). The Primary Oxygen Supply is still maintaining a suit pressure of 4.3 psid and can maintain that differential pressure during a normal rate of airlock repressurization.
2 The repress is stopped at 5.0 psia to configure for continued repress.Note that the suit absolute pressure is at 9.3 psia. The crewmember then switches from "PRESS" to "IV."
3 The suit pressure remains at approximately 9.3 psia, but the suit-to-chamber differential pressure drops as the chamber/airlock pressure increases.
4 When the suit-to-chamber delta P reaches 1 psi, the Primary Oxygen Supply (POS) begins controlling the suit pressure at 1 psi, so the suit absolute pressure begins to climb again.
5 When sea level (ambient) pressure is reached in the chamber, the suit is 1 psi above ambient pressure at approximately 15.7 psia.
6 The crewmember moves the O2 Actuator to "OFF" and opens the Purge Valve to vent the suit to ambient pressure for suit doffing.
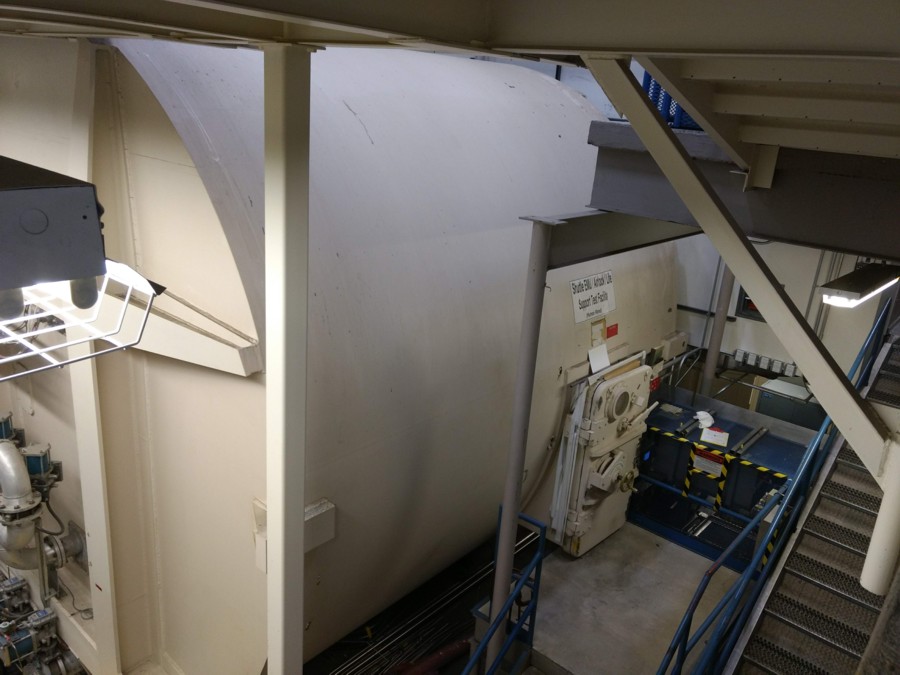
This is a view of the entrance to the Shuttle Cabin Environmental Test Article or ETA for short. It was the last large chamber moved into Building 7.
(The SSATA was a smaller pressure vessel add onto the 20-ft Chamber after the ETA was moved in.) The pressure vessel is made of aluminum.
Although the outer configuration is a horizontal cylinder with flat ends, the interior configuration matched the Shuttle cabin with the nose section at this
end and the airlock in "cargo bay" configuration at the other end as shown in the next photo. Note the weld seam between the end plate and the
cylinder; it looks like that end plate is about 3" - 4" thick with additional "I"-beam reinforcement. I'm not sure how the the cylinder walls are, but they
must be several inches thick.
In 1992 a test was proposed to evaluate a Regenerable Carbon Dioxide Removal System (RCRS) for installation in a Shuttle Orbiter cabin. The RCRS was proposed to support long Shuttle missions which otherwise would have required so many LiOH (lithium hydroxide) cannisters for CO2 removal that the shuttle cabin would be full of the heavy cannisters. The test was intended to show that the RCRS could support a crew of seven for a sixteen day mission.
It was decided that the test would be in two eight-day segments so that seven women could be in half the test, and then seven men could do the final half. Our boss didn't want to mix crews. He also didn't want the women to have access to a phone, but we wired a land line into the chamber anyway. The women called the test the "Mockup Lockup." The test was started in late April and was complete in May of 1992.
I was told that one of the RCRSs was to be installed in Columbia, and that was the only one installed.
Some details and photos from the test are here: The Mockup Lockup"
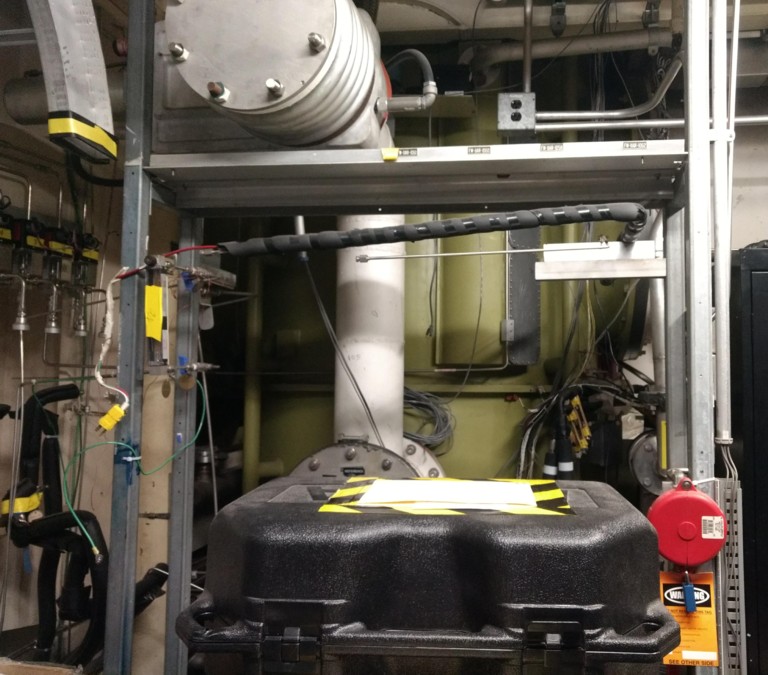
The ETA Airlock that has the same internal volume as the Shuttle Airlock and has the same spacecraft power and control panels and the depress and repress valves that the Shuttle Airlock has. It is olive drab colored vertical cylinder and it's hard to see and even to get to because of all the surrounding facility systems and structures. It operated at pressures from ambient (14.7 psia) down to 100 microns of mercury pressure (0.001 mmHg pressure). I have some good views from the Shuttle cabin side, so maybe I'll add them some day.
Ever Shuttle astronaut assigned to EVA duty for each mission went through a vacuum training run to prepare for and become familiar with the procedures for operating the EMU and the Airlock in combination and to be familiar with the characteristics of the equipment before they were actually in space doing their EVA responsibilities.
- Posted 12/18/19 JSC Building 7A Spacesuit Displays - - - - Skipper Family Magazine Index
|